Air preheater

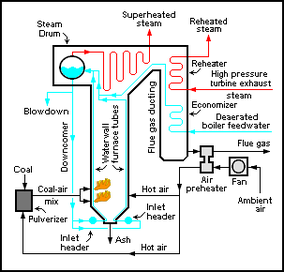
Schematic diagram of a steam generator in a conventional coal-fired power plant.
An air preheater (APH) is a general term to describe any device designed to preheat the combustion air used in a fuel-burning furnace for the purpose of increasing the thermal efficiency of the furnace.
In particular, this article describes the combustion air preheaters for the large fuel-burning furnaces used to generate steam in thermal power plants. The air preheater increases the steam generator's thermal efficiency by preheating the combustion air with heat recovered from the hot combustion flue gases (see the adjacent diagram).
Types
The two most often used categories of air preheaters in thermal power plants are regenerative air preheaters and tubular air preheaters.[1][2][3][4]
Regenerative air preheaters
The two most common types of regenerative air preheaters are
- The rotating-plate regenerative air preheater, often referred to as a RAPH. The RAPH was invented by Fredrik Ljungström, who was a Swedish engineer, and is also called a Ljungström air preheater.
- The stationary-plate regenerative air preheater, often referred to as a Rothemuhle because Rothemühle is the German town where the original manufacturer produced them for many years.
Regenerative air preheaters may also be categorized as recuperators, which are special types of heat exchangers designed to recover or reclaim heat in order to reuse or recycle it.
Rotating-plate regenerative air preheater
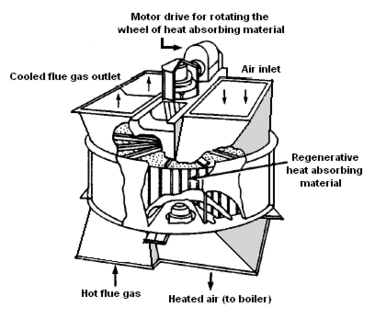
A typical rotating-plate regenerative air preheater.[2]
The rotating-plate air preheater (RAPH) consists of a central rotating-plate element installed within a casing that is divided into sectors. There are three basic designs for the rotating-plate element:[5][6]
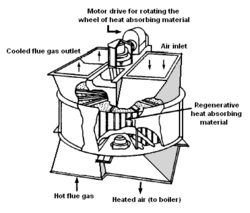
A typical rotating-plate regenerative air preheater.[2]
- The bi-sector design has two sectors.
- The tri-sector design has three sectors.
- The quad-sector design has four sectors.
In the tri-sector design, the steam generator's hot flue gas flows through the largest sector (usually spanning about half the cross-section of the casing) and transfers some of its heat into the heat-absorbing material within the rotating wheel element. The cooled flue gas is then routed to further treatment in dust removal and other equipment before being vented from the flue gas stack. Ambient air is blown through the second, smaller sector by a centrifugal fan and absorbs heat from the heated material as it rotates through that smaller sector. The heated air then flows into the steam generating furnace as combustion air. The third sector is the smallest one and it heats a portion of the ambient air which is then routed into the coal pulverizations and is used to transport the coal-air mixture to coal burners. Thus, the total air heated in the RAPH provides: heated primary combustion air, heated air to remove moisture from the pulverized coal and carrier air for transporting the pulverized coal to the coal burners. Since the flue gas pressure is lower than the pressure of the air being heated, there is some small leakage (between the sectors) of flue gas into the air.
The bi-sector design is used in thermal power plants burning fuels (such as oil or gas) that do not require pulverizing or removal of moisture and therefore have need for heated air other than for combustion air.
The quad-sector design has a large sector heated by flue gas and three air-heating sectors: one is for the combustion air and that sector is flanked by two smaller air sectors. In applications such as circulating fluid bed (CFB) combustion systems where the differential between the air pressure and the flue gas pressure is even higher than in a conventional coal-fired steam generator, flue gas pressure, such a design is ideal since it acts to reduce the leakage of air into the flue gas.[6]
The rotating wheel element rotates quite slowly (around 3-5 revolutions per minute) to allow optimum heat transfer first from the hot exhaust gases to the element and then, as it rotates, from the element to the air in the other sectors.
Construction features
The heat-absorbing material in the rotating wheel element consists of vertical corrugated plates pressed into steel baskets, with sufficient space between the plates for the flue gas to pass through. The plates are corrugated to provide more surface area for the heat to be absorbed and also to provide needed rigidity. The baskets are designed to be replaceable as needed.
The vertical shaft that rotates the wheel is supported on thrust bearings at the lower end lubricated with an oil bath that is cooled by water circulating in coils inside the oil bath. Cooling of the bottom end of the shaft is needed since that is where the hot flue gas enters the preheater. The top end of the shaft has a simple roller bearing to hold the shaft in a vertical position.
Radial supports and cages for holding the corrugated plate baskets in position are attached to the rotating shaft. Radial and circumferential seal plates are also provided to minimize leakage of flue gas or air between the sectors.
For cleaning of the baskets while in operation, steam jets are provided to blow any fly ash (deposited by the flue gas) into an ash hopper below the preheater.
The rotating shaft is driven by a motor and gearing. To avoid uneven thermal expansion and contraction resulting in damage to the rotating wheel, the rotation must be started before starting the steam generator and must also be kept in rotation for some time after the steam generator is shut down.
The baskets of corrugated plates are subject to abrasive and corrosive wear from the fly ash and corrosive gases in the flue gas. Hence frequent replacements are required and new baskets are always kept on hand and ready for use.
Stationary-plate regenerative air preheater
The heat absorbing element in this type of regenerative air preheater is stationary rather than rotating. Instead, the air ducts in the preheater are rotated so as to alternately expose sections of the heating absorbing element to the upflowing air.
The hot flue gas enters at the top of the preheater and flows down through those exposed sections of the stationary heat-absorbing element that are not blocked by the rotating air outlet ducts, thus heating those sections of the stationary element. As the air ducts slowly rotate around, they pass over the heated sections and the incoming air is heated as it flows upward through those heated sections.
As indicated in the adjacent drawing, there are rotating inlet air ducts (inside the outer casing) at the bottom of the stationary heat absorbing element as well as the rotating outlet air ducts at the top of the stationary element.
The basic heat transfer principals of the stationary-plate regenerative preheater are the same as for the rotating-plate regenerative preheater. The table below provides a comparison of some design parameters between the rotating-plate and stationary-plate preheaters:
Rotating-plate | Stationary-plate | |
---|---|---|
Revolutions per minute | 1.5 – 4.0 (a) | 0.7 – 1.4 (b) |
Gas flow area, % of total | 40 – 50 | 50 – 60 |
Air flow area, % of total | 35 – 45 | 35 – 45 |
Seal section area, % of total | 8 – 17 | 5 – 10 |
(a) Revolutions per minute of the rotating plate element (b) Revolutions per minute of the rotating air ducts |
Tubular type
Tubular air preheaters may have a number of configurations:[2][8][9]
- A bundle of vertical tubes through which the flue gas flows downward (see adjacent diagram) and exchanges heat with ambient air flowing horizontally across the exterior of the tubes. Baffles are usually provided so that the air flows across the tubes a number of times. For example, as shown in the adjacent diagram, the air flow across the tubes three times and is referred to as 3-pass tubular air preheater.
- The same as (1) above except that the flue gas flows upward rather than downward.
- A bundle of horizontal tubes through which the air flows and exchanges heat with the hot flue gas flowing downward across the tube bundle. In some designs, there may be three separate horizontal tube bundles one above the other. The air enters the lower tube bundle from the right-hand side, exits on the left-hand side and then enters the middle tube bundle on the left-hand side and exits on the right-hand side. Finally, the air enters the upper tube bundle on the right-hand side and exits on the left-hand side. In essence, such a design is similar to the 3-pass design of (1) above except that the air is in the tubes rather than outside the tubes.
A number of new circulating fluid bed (CFB) and bubbling fluid bed (BFB) steam generators are using tubular air preheaters, which avoids the air leakage associated with regenerative air preheaters.
Dew point corrosion
The dew point of air or any other gas containing water vapor usually refers to the temperature (for a given pressure) at which the air or gas is saturated with water vapor. That means that the air or gas is at the point where the water vapor will start to condense into liquid water if the temperature is lowered beyond that point.
As a broad generality, the combustion flue gases from steam generators fueled by coal, fuel oil, natural gas, or biomass are composed of carbon dioxide (CO2) and water vapor (H2O) as well as nitrogen and excess oxygen remaining from the intake combustion air. Typically, more than two-thirds of the flue gas is nitrogen. The combustion flue gases may also contain small percentages of air pollutants such as particulate matter, carbon monoxide, nitrogen oxides, and sulfur oxides in the form of gaseous sulfur dioxide (SO2) and gaseous sulfur trioxide (SO3). The SO3 is present because a portion of the SO2 formed in the combustion of the sulfur compounds in the steam generator's furnace fuel is further oxidized to SO3 as the flue gas travels through the superheater and reheater sections of the steam generator (see the above diagram of a steam generator). The gas phase SO3 then combines the vapor phase H2O to form gas phase sulfuric acid H2SO4:[10]
- H2O + SO3 → H2SO4
Because of the presence of gaseous sulfuric acid, the dew point of most flue gases is much higher than the water dew point of air and the flue gas dew point is referred to as the acid dew point. That is the flue gas temperature at which acid will begin to condense out of the flue gas if the temperature is lowered beyond that point. For example, a flue gas with 5 volume % water vapor and containing no acid gases has a water dew point of about 32 °C (90 °F). The same flue gas with the addition of only 0.01 volume percent of SO3 will have an acid dew point of about 118 °C (244 °F).[11]
The acid dew point of a combustion flue gas depends upon the composition of the specific fuel being burned and the resultant composition of the flue gas. Given a flue gas composition, its acid dew point can be predicted fairly closely. As an approximation, the acid dew points of flue gases from thermal power plants range from about 120 °C to about 150 °C (250 to 300 °F).
All of the air preheater types incur erosion problems to some extent from the fly ash particles in the flue gas. If the hot flue gas temperature in an air preheater is lowered to below its acid dew point, then the air preheater also incurs corrosion problems which can be quite severe. That is especially true of the tubular air preheaters. For that reason, many air preheaters have a means for the air to partially bypass the air preheater (see above tubular air preheater diagram) so that the amount of heat exchange can be controlled to avoid lowering the flue gas temperature below the acid dew point.
To mitigate dew point corrosion, the tubular air preheaters may use ceramic or Teflon-coated tubes and the regenerative air preheaters may use special corrosion-resistant steels or enameled materials.
The addition of limestone (CaCO3) into circulating fluidized bed (CFB) steam generators results in capturing 95% or more of the gaseous SO2 in the combustion product gases as solid calcium sulfate (Ca2SO4) and that occurs before the SO2 has time to be further oxidized to SO3. Thus, the acid dew point of the flue gas from a CFB steam generator is higher than from conventional thermal power plant steam generators. That means that the air preheaters in CFB units have considerably less dew point corrosion problems. That may also be one of the reasons why a number of the newer CFB units are using tubular preheaters.
References
- ↑ Sadik Kakaç and Hongtan Liu (2002). Heat Exchangers: Selection, Rating and Thermal Design, 2nd Edition. CRC Press. ISBN 0-8493-0902-6.
- ↑ 2.0 2.1 2.2 2.3 Course SI:428A Online publication of the U.S. Environmental Protection Agency's Air Pollution Training Institute, known as APTI (Scroll down to page 23 of 28)
- ↑ Sadik Kakaç (Editor) (April, 1991). Boilers. Evaporators and Condensers. Wiley Interscience. ISBN 0-471-62170-6. (See Chapter 8 by Z.H. Lin)
- ↑ Lawrence Drbak, Patricia Boston, Kalya Westra, and R. Bruce Erickson (Editors) (1996). Power Plant Engineering (Black and Veatch). Chapman & Hall. ISBN 0-412-06401-4.
- ↑ The Ljungström® Air Preheater
- ↑ 6.0 6.1 Ljungström® Air Preheater Arrangements
- ↑ Prabir Basu, Kefa Cen and Louis Jestin (1999). Boilers and Burners: Design and Theory, 1st Edition. Springer. ISBN 0-387-98703-7.
- ↑ 8.0 8.1 http://www.egcfe.ewg.apec.org/Documents/Costs&EffectivenessofUpgradingOlderCoal-FiredPowerPlantsFina.pdf Costs and effectiveness of upgrading and refurbishing older coal-fired power plants in developing APEC economies] Asia-Pacific Economic Cooperation (APEC) Energy Working Group, Expert Group on Clean Fossil Energy, June 2005
- ↑ Performance Analysis of Primary Air Heater Under Particulate Condition in Lignite-Fired Power Plant Journal of Engineering, Computing and Architecture, Vol. 1, Issue 2, 2007
- ↑ Predicting Sulfuric Acid Emissions from Power Plants]
- ↑ Burning Sulfur Compounds A publication of the Banks Engineering Company of Oklahoma.